Fluid Bed Dryer (FBD) Machine | Fluid Bed Dryer Manufacturer in India
Sterial Machinery is one of the leading Fluid Bed Dryer (FBD) Machine Manufacturer in India, offering supreme quality, efficient, and creative drying solutions for pharmaceutical machinery and equipment. Our Fluid Bed Dryer is designed with advanced technology, providing optimal drying versions for materials such as powders, granules, and other particulate products.
The FBD machines manufactured by Sterial Machinery are known for their durability, fuel efficiency, and user-friendly procedure. Our fluid bed dryers produce uniform drying by breaking solid particles in a flow of wild air, allowing faster drying times and enhancing product quality.
As a top Fluid Bed Dryer Manufacturer in India, we prioritize safety and adherence to global standards, confirming each machine is built to perform always while preserving strict hygiene and safety protocols. Our expert engineering team customizes FBD machines to meet the specific essentials of different industries, whether it’s batch drying or continuous procedures.
With elements like easy-clean designs, exact temperature control, and automatic process monitoring, Sterial Machinery’s fluid bed dryers secure operating efficiency and reduce downtime. We pride ourselves on providing excellent customer service and technical support, helping clients from production to maintenance. Choose Sterial Machinery for trustworthy and advanced fluid bed drying solutions that expand productivity and hold excellent quality standards.
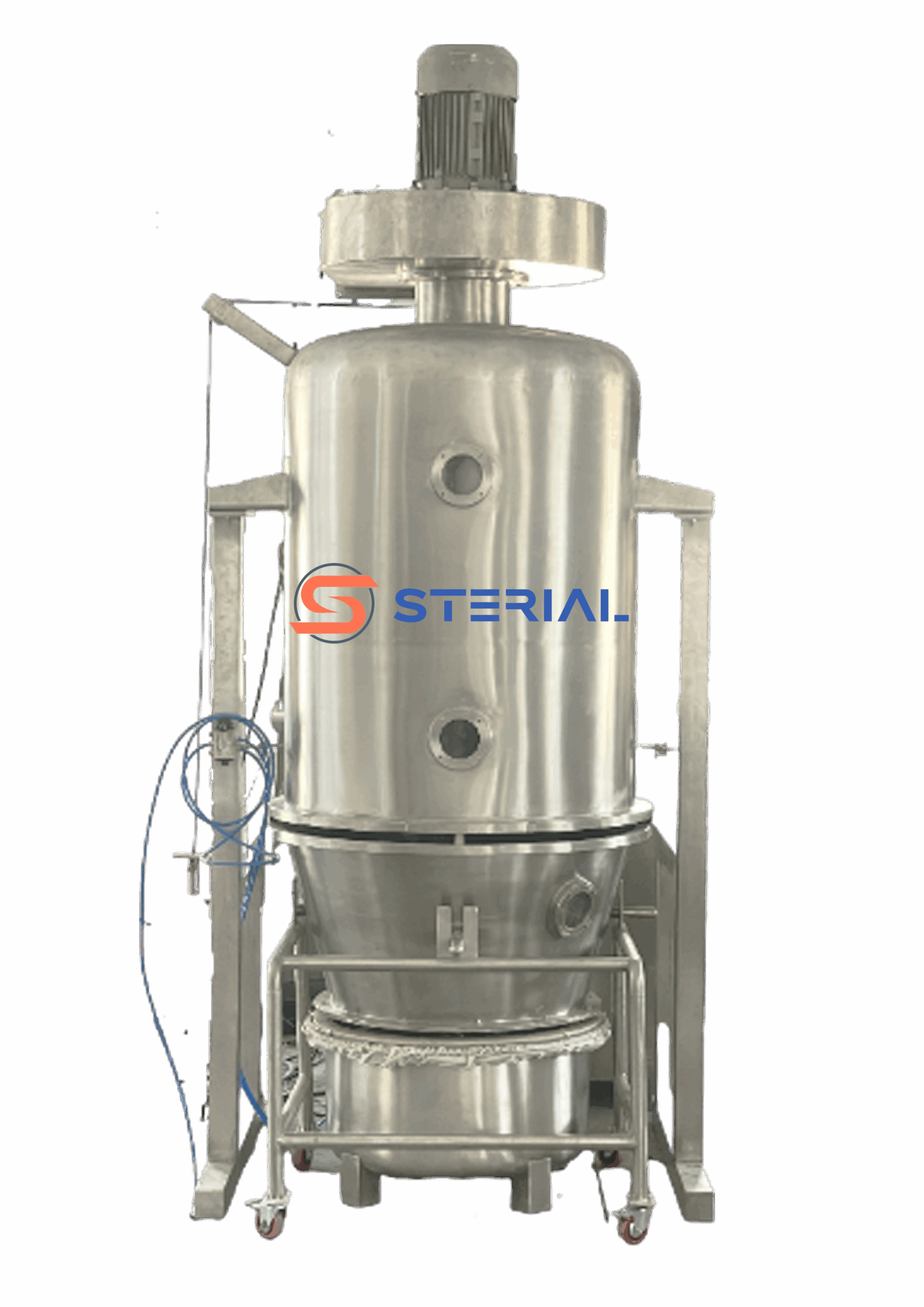
Application & Process:
Sterial Machinery has adopted a new concept of GMP Regulation and fluid bed technology for the production of a Fluid Bed Dryer, Fluid Bed Processor which yields improved performance. The drying time in the machine is much less than in the conventional model. There is minimum involvement of manual labor simplified maintenance and utilize modular construction techniques to provide flexible installation options.
The Fluid Bed Dryer is a two-piece unit which is manufactured from SS316 stainless steel. The process of mixing Dry powders, Agglomeration, and Drying is carried out in one unit Fluid Bed Dryer.
Fluid bed dryer finds extensive usage in pharmaceutical industries to reduce the moisture content of pharmaceutical granules and powder. It is also known as a fluidized bed dryer. The machine has excellent gas particle constant which enables it to produce a high rate of moisture removal that results in high mass and heat transfer rates.
- Main unit is mounted on two no’s ss square pipe with c type structure on back for better mounting.
- The Pillar are made of SS 304 Square tube.
- 4 nos ss 304 pads are provided at bottom for better grip.
- All pillars will be at Ground floor with Anchor Fastener.
- Pneumatic (cylinder) for bag shaking, bag UP/down.
- Fluidized Bed Chamber [Main Housing], retarding chamber and filter bag housing made from Stainless Steel grade SS 316.
- Expansion Chamber is in single piece construction and is fully locked with only inflatable seals with interlock.
- Chamber will be provided with an inspection window duly sealed with toughened glass.
- Chamber will be provided with a light window duly sealed with toughened glass.
- Filter bags are made from Satin Clothes.
- Filter Bag fixing through SS Fixing ring and equipped with an inflatable seal.
- Top dish made from Stainless Steel grade SS 304.
- Three Level Pneumatically Operated Inflatable seals
- Three different cylinders one is for filter bag up/down and second is for shaking and third one is for rope locking as a failsafe design
- Inner surface of the container will be mirror finished.
- Outer surface of the container will be 180 grit finishes
- Horizontal Explosion flap fixed with a thin aluminum sheet
- Product Container made from Stainless Steel SS 316.
- Perforated air distribution plate along with Dutch weave mesh will be provided with quick opening toggle clamp.
- Glass window will be provided on the product container.
- Sample collection port will be provided
- Container will be on movable trolley made of SS 304 and is fixed on PU castor.
- Inlet Chamber is made of Stainless Steel SS 304
- Inlet Chamber is mounted on main Pillar with adjustable type of design.
- Typically designed air path for proper fluidization of material
- Inlet chamber having a temperature sensor for measuring of inlet air temperature
- Product Container sealing through pneumatically actuated Inflatable Seal made from food grade and necessary pneumatic interlocks to ensure fail safe interlocking mechanism.
- Filter Bag Sealing.
- Filter Bag sealing through pneumatically actuated Inflatable Seal made from Silicon and necessary pneumatic interlocks to ensure fail safe interlocking mechanism.
- Filter Bag Shaking Device.
- Filter Bag Shaking through pneumatically actuated device.
- Filter Bag locking through the pneumatically actuated cylinder with rope with fail- safe mechanism and to release the bag for cleaning.
- Design is cGMP – Current Good Manufacturing Practices compliance.
- Design is cGMP – Current Good Manufacturing Practices compliance.
- Available in 30kg, 60kg, 120kg, 250kg, 300kg, 400kg, 500kg.
- Electrically or Steam Heated Drying
- Inlet AHU with Air Filters
- Exhaust air blower with dynamic balance fan.
- Automatic Temperature controls for Inlet Air and Process cycle time controls.
- View Glass Provision for Fluidization and Shaking operation
- Food Graded Silicon Inflatable Tube Seal for the Product Container sealing.
- Manual Push Button Type (RYB) Control Panel on Machine
- Machine consisting with Bottom Chamber, Product Container with Trolley, Expansion Chamber, Exhaust Blower with SS Cover & Air Handling Unit.
- Sampling Pot on Product container
- Easily Attachable with vacuum transfer system
- Electric and Pneumatic controls panel.
- Extra Product Container Trolley
- Flameproof Electrical
- VFD Driver for Blower
- PLC with HMI Touch Screen
- Auto Bag Shaking
- Auto Loading System, Vacuum Transfer
- Ducting & Elbow
- Blower motor trip
- Emergency stop
- Dry cycle over (PLC)
- Batch Complete (PLC)
MODEL | FBD 30 | FBD 60 | FBD 120 | FBD 200 | FBD 250 | FBD 300 | FBD 400 | FBD 500 |
Container Volume (Liters) | 90 | 200 | 400 | 650 | 800 | 960 | 1250 | 1600 |
Max. Batch Capacity (0.5bd) KG | 20-30 | 40-60 | 80-120 | 160-200 | 200-250 | 250-300 | 300-400 | 400-500 |
Blower Motor HP | 7.5 | 10 | 20 | 20 | 25 | 30 | 40 | 50 |
Air Flow (CFM) | 706 | 1060 | 1880 | 2590 | 3235 | 3250 | 3825 | 4000 |
Steam Consumption (kg/hr) | 50 | 80 | 140 | 216 | 250 | 280 | 350 | 400 |
Electric Heater (KW) | 20 | 36 | 60 | N.A. | N.A. | N.A. | N.A. | N.A. |
- Dying Temperature: 35-80 c*
- Electrical Supply: 415v , AC, 50Hz*